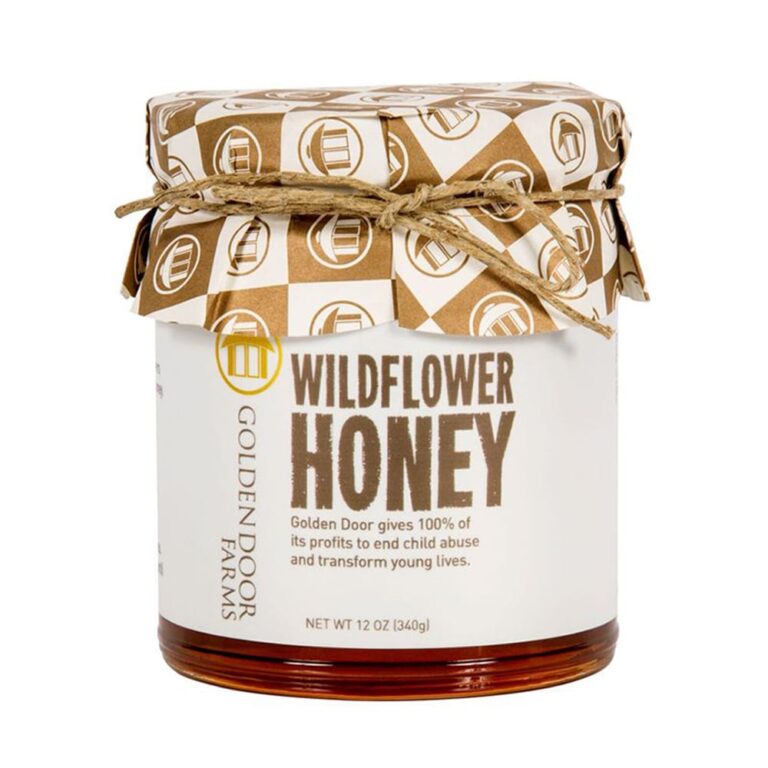
Artisan Food Labels
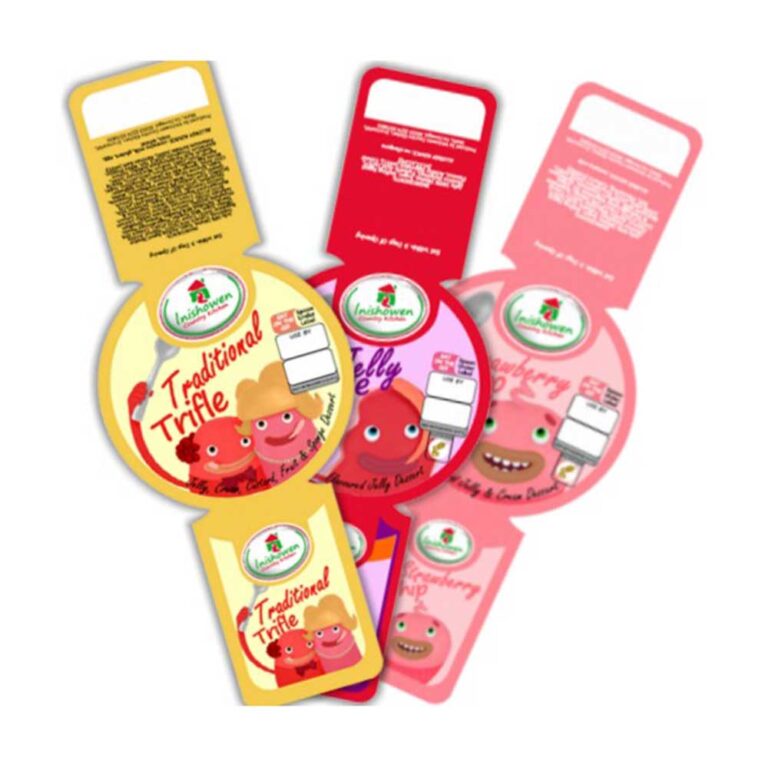
Frozen Food Labels
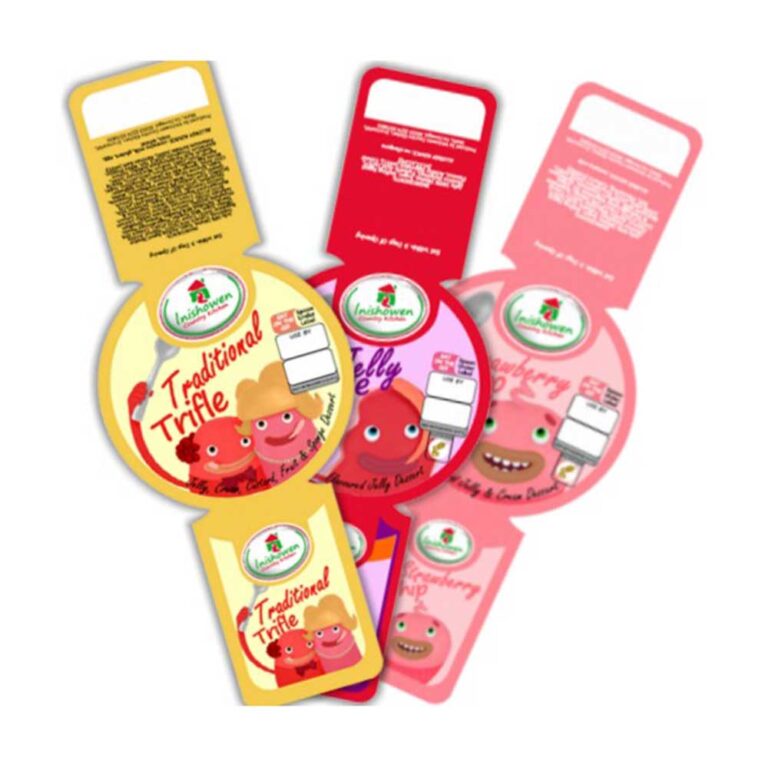
Pre-Packed Food Labels
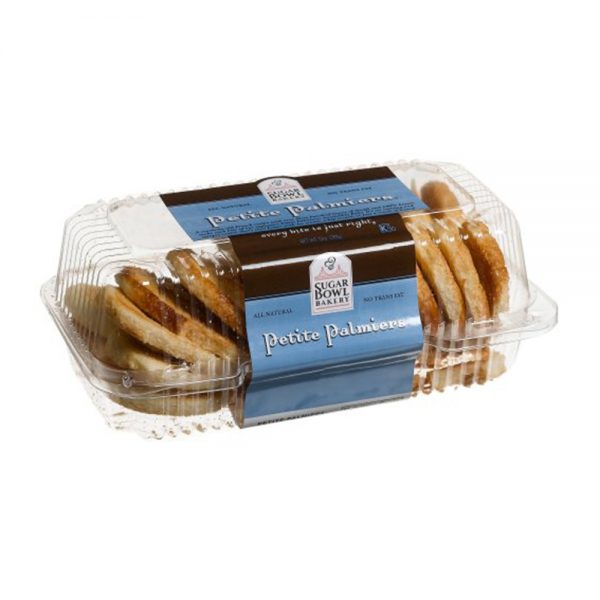
Bakery Labels
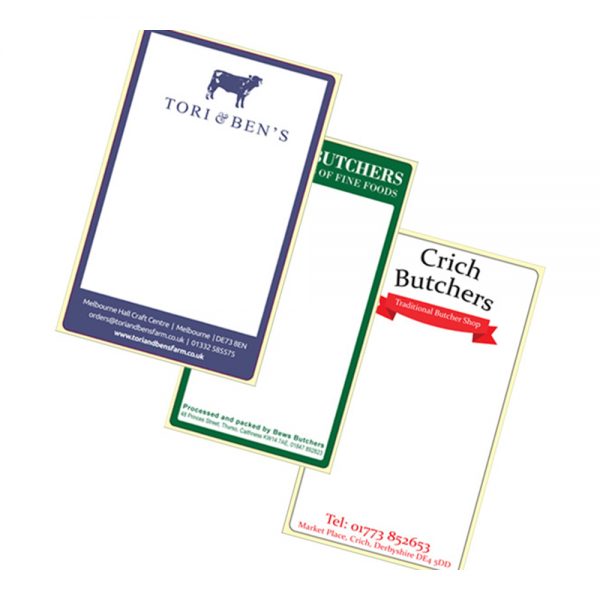
Butchers Labels
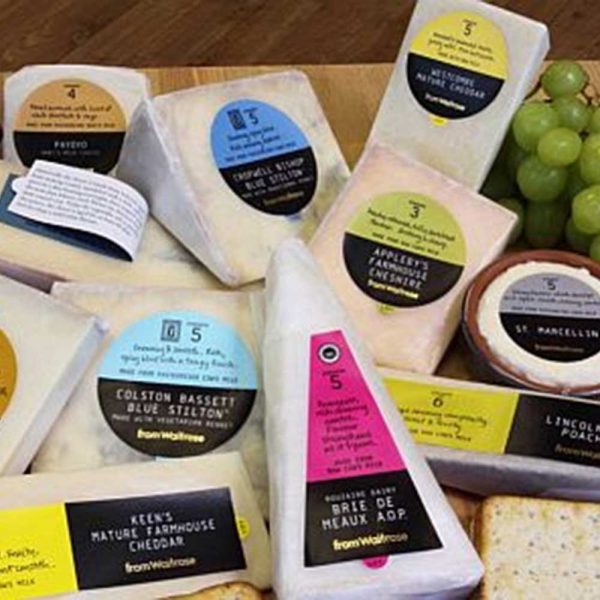
Dairy Product Labels
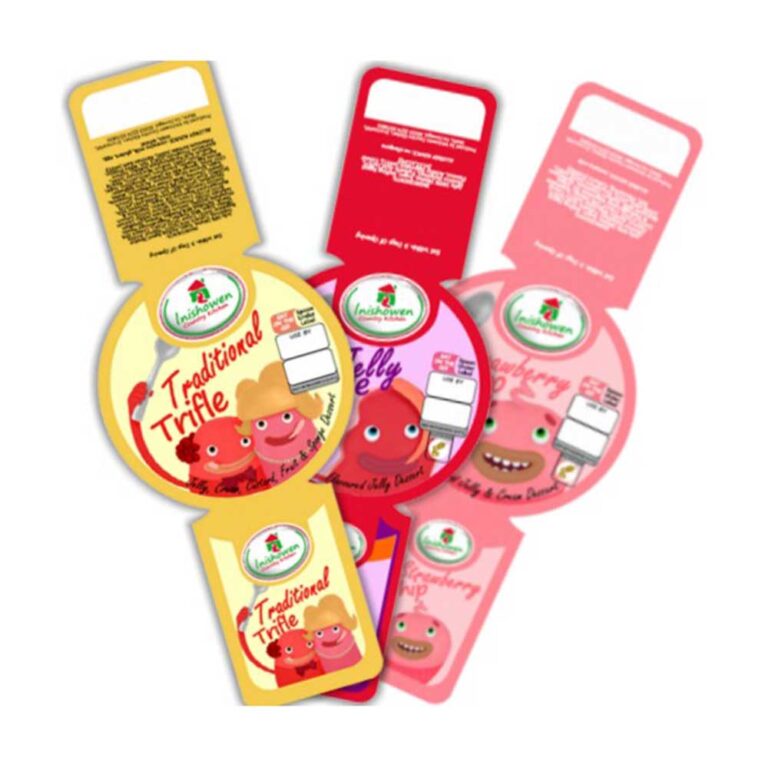
Dessert Labels & Pudding Labels
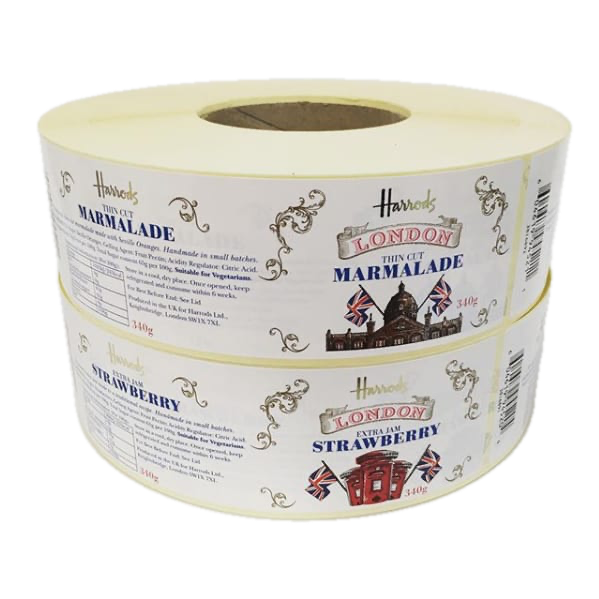
Jam Jars
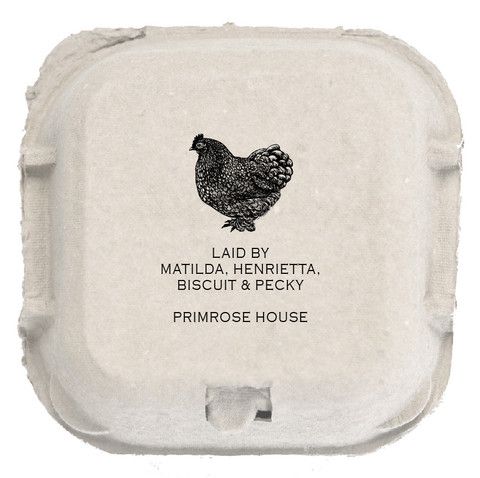
Egg Packing Labels
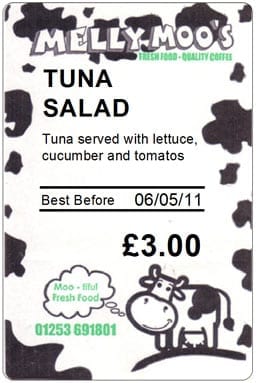
How do you choose between direct thermal or thermal transfer printing?
Thermal printing is a digital printing process, which produces printed images by selectively heating coated heat-sensitive paper – usually curing the paper to turn it black where heated (although other colours can be achieved).
Thermal transfer printing uses a coated ribbon to produce durable, long-lasting pictures and text on a variety of materials. Direct thermal printing creates images directly onto the material; this makes direct thermal more sensitive to light, heat and abrasion and reduces its lifespan.
Choosing direct thermal or thermal transfer printing? Well, that because:
The decision to choose direct thermal or thermal transfer printing is based on the performance you need from your adhesive labels. The difference is that Direct Thermal printers don’t use ink, toner or ribbon. This makes them cheaper to operate compared to inkjet, laser, impact and thermal transfer printers (which uses a consumable ribbon). It is a more environmentally friendly method too as there is no need to dispose of the used ink ribbons, so reducing waste.
The consequence of not using ink, however, is that the labels will lack lifespan. The labels remain scannable for up to 6 months if well stored such as would be the case in a distribution centre. They are suited to short lifespan applications such as courier distribution, food and short life processes.
On the other hand, thermal transfer printers utilise a thermal ribbon, which when heated, delaminates the wax or resin onto the material face forming the image wanted. This provides an image of high quality and excellent durability and lifespan. Another benefit is that thermal transfer can be used on a wide range of materials. Direct thermal printing can only be used with direct thermal papers or plastics, the latter being extremely expensive.
These different materials may affect the durability of the labels. E.g. polyester is waterproof, scratch resistant and has an excellent durability, therefore, the label having long-term outdoor durability as well as being a permanent acrylic adhesive.
You can see some of them below some of the materials used in thermal transfer printer that allows durability to vary:
Positive ID Labelling can provide thermal printers capable of printing direct thermal or thermal transfer labels for you. For more guidance or information, call us on 01332 864895Sakshi Pushpinder
Get free advice from one of our print experts by calling: 01332 864895 or fill in your details below.
"*" indicates required fields